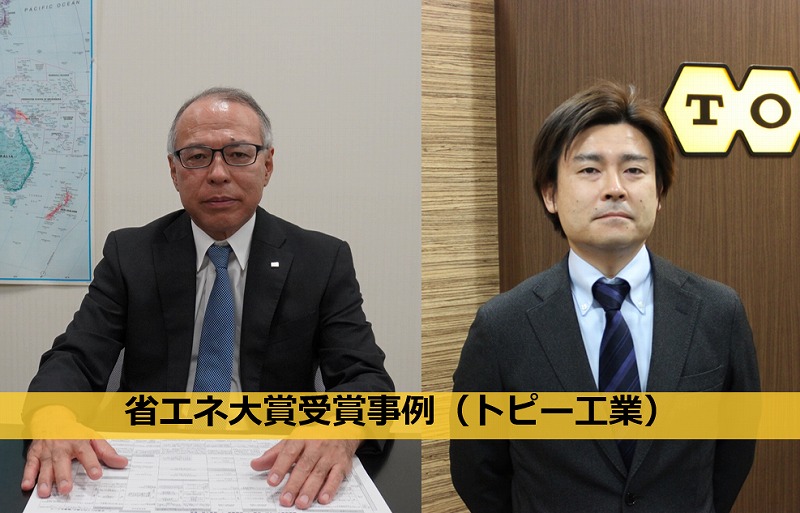
省エネ担当者だけにとどまらない全員参加の省エネ活動は、多くの企業が目指す状態であるものの、実際に達成できるケースは多くありません。
生産や開発が優先されてしまうことで、省エネ活動は一部の担当者による取り組みに限られがちになるからです。
自動車用ホイールなどを手がけるトピー工業株式会社(東京都品川区)も、そうした課題を抱えていた企業の一つです。
2011年の東日本大震災によって産業用の電気代が急騰したことをきっかけに、本格的な省エネ活動を始めた同社。まずは建設機械用部品を生産する神奈川製造所での電気代削減を急務としました。
「神奈川製造所で消費するエネルギーの8割が電力だったため、コスト削減に向けて電力削減は必須でした」。
こう振り返るのは、当時神奈川製造所の所長を務めていた木下浩幸氏(現・専務取締役)。
トピー工業株式会社の木下氏
活動開始当初は、エネルギー管理者が主体となりコンプレッサーを中心とする機器の効率改善などで一定の成果を上げました。
しかし省エネ担当者たちだけで手をつけられる範囲は限られたため、改善案も枯渇。省エネ活動は壁に突き当たってしまいます。
そこで2014年には、省エネ担当者の権限を強化する動きを取りました。部門横断で対策を打つ権限を持った「省エネマイスター」と呼ばれるポストを設置したのです。
強い権限を持った省エネマイスターを中心に、生産者なども巻き込んだ活動が実を結び、エネルギー消費量を17%削減、契約電力を27.5%低減するなどの成果を達成。さらに2017年度の省エネ大賞(省エネルギーセンター会長賞)を受賞するほどの評価を得ました。
トピー工業株式会社による省エネ施策の一覧(出典:トピー工業株式会社資料を基にエネチェンジ作成)
木下氏の掛け声で省エネに舵を切った神奈川製造所だが、終始トップダウンで事を運んだわけではありません。
省エネの気運や実施しやすい環境をトップダウンで作りつつも、あくまで具体的な改善策の検討や実施については、ラインを熟知する現場担当者による自主性を重視したバランス感がポイントです。
木下氏に加え、初代の省エネマイスターとして施策を推進した齊藤和信氏(現:業務改革推進室・SF推進G長)に話を聞いた。
トピー工業株式会社の齊藤氏
省エネのきっかけ、顧客企業からの支援
電力削減に向けて本格的に動き出した2012年頃を振り返り、木下氏はこう話します。
「とにかくコスト削減が第一課題でした。弊社の顧客で省エネに先進的に取り組まれている大手企業から、色々と教えていただきました」。
その顧客企業の省エネ推進者を神奈川製造所に招き、様々なアドバイスを受けたほか、所員全員を対象にした講演会を開催するなどの支援を受けたといいます。
「“全員参加の省エネ活動“に向けたきっかけを与えていただいた。所員全員で取り組もうという空気づくりにもなりました」(木下氏)。
電力消費の可視化に着手
省エネ活動を始めた当初の課題について、木下氏はこう話します。
「最初はどうやってエネルギーを削減していくか頭を悩ませました。設備ごとの電力を削減することで、どれだけの投資対効果を得られるかはやってみないと分からない、という状態からのスタートでした」。
そこで着手したのが電力消費の「見える化」です。省エネマイスターが主導する形で、電力量計を各ラインに設置し電力使用量を可視化しました。
スモールスタートとして、一部の生産ラインの見える化から始め、実際に効果が出るか検証。電力消費の可視化によって、現場作業者の省エネに対するモチベーション向上につながるといった結果を確認した上で、最終的に284台の電力量計を設置するに至ったという。
しかしこの「見える化」施策では、蓄積されたデータをエネルギー管理者が都度分析し、結果を現場に展開するという時間のロスが発生してしまいます。
つまりデータをリアルタイムで確認しながら改善策を検討する、といったスピード感あるPDCAを回すことが難しいのです。
「また問題がありそうだと分析者が感じたところしか深堀しないので、省エネ課題の発見量も増えづらい状態でした」(齊藤氏)。
こうした課題感を感じていた現場の作業者から提案された打ち手が、データの「見せる化」です。
エネルギー消費の推移を「いつでも」「誰でも」「かんたんに」把握できることを目的とした「見せる化」システムを2016年に導入しました。
同システムでは、電力の推移を事務所内のサイネージやタブレットなどにリアルタイムで表示。さらにベンチマークとする数値との比較も一目でできるため、「いつ」「どれだけ」のエネルギーをロスしたかもすぐに分かるといいます。
「作業者が苦手な分析と改善施策の効果計測を自動化することで、省エネがどんどん進むようになりました」(齊藤氏)。
システムの構築は、ほぼ自社で手掛けたため開発にかかる費用や工数も大きく削減できたといいます。
見せる化システムの概要(出典:トピー工業株式会社資料より)
見せる化システムの特徴(出典:トピー工業株式会社資料より)
見せる化の事例
見せる化システムの活用例の一つが、電力のピークシフトです。
当時の神奈川製造所には多数の設備があり、バッチ処理の電力需要の高い設備を複数同時にスタートさせた場合、電力のデマンド値を引き上げてしまうことがありました。
そこで所内のサイネージやタブレットによって、それぞれ離れた場所にある炉の電力需要をリアルタイムで確認できるようにしました。抵抗加熱炉の昇温開始可否を個々の作業者が判断できるようになったため、契約電力の低減につながったといいます。
また生産計画を管理するエクセルファイルに、デマンドピークを自動算出する機能も持たせました。ファイルに入力される生産量などの数値に応じて、稼働ラインのデマンドが自動で表示される仕組みです。
表示される電力数値は、許容範囲であれば「白」、見直しが必要であれば「赤」で表示するなど、生産管理と電力需要の関係が一目で分かるよう工夫しました。
生産計画に使用しているエクセルファイル例(出典:トピー工業株式会社資料を基にエネチェンジ作成)
こうして生産管理部門は、電力需要も踏まえた生産管理を実施できるようになったのです。
上記を含む見せる化施策の前は、生産活動を優先して余裕を持った契約電力(4,000kW)を設定していたものの、施策後は以下のように段階的に契約電力を低減していきました。
- 2015年:3,300kW
- 2016年:3,000kW
- 2017年:2,900kW
省エネマイスターの個別指導、意識改革に貢献
見える化・見せる化システムによって効果を実感できる環境を整えたことで、省エネがより身近になったわけですが、成功の要因はそれだけではありません。
「苦労したのは省エネに対する意識変革の部分」と齊藤氏は振り返ります。
「現場の作業者が自主的に省エネに取り組むことがとにかく最優先です。見える化や見せる化はその手段に過ぎません」(齊藤氏)。
自主的な取り組み促進に向け大きく貢献したのが、省エネマイスターによる個別指導です。
「たとえば見せる化システムを踏まえた省エネを工場の現場作業者の方に教える時は、改善のノウハウや見せる化システムの使い方も直接レクチャーしました」(齊藤氏)。
一方で生産管理部門のように、省エネに馴染みが薄い場合はより深く入り込みます。
「生産管理の方々は、省エネに注力するようトップダウンで指示を受けているものの、どうすべきか分からないという状態でした」(齊藤氏)。
そこでさまざまな勉強会を開いたほか、成功イメージを具体的に伝えていきました。
「たとえば“この施策で契約電力を平準化できるとこれくらい電気代が下がりますよ”、“このバランスであれば出荷時期も遅れませんよ”といった具合です」(齊藤氏)。
この地道な取り組みによって、「省エネもそんなに難しくなさそうだ」という認識が広がりました。生産管理部門で電力平準化も考慮した生産計画を立てられるようになっていったといいます。
しかしどの企業でも、省エネに興味関心があるというスタッフは必ずしも多くありません。こうした意識改革に苦労はなかったのだろうか?
「省エネを頑張ってみても良いかなという人は、どの職場にも必ず1人か2人はいます。最初はその方々に特に集中的に教育をして“省エネキーマン”になっていただき、次回からはそのキーマンから後輩などに伝授してもらいます」(齊藤氏)。
その段階で齊藤氏の個別指導が終わり、各集団による自走が始まるという流れだ。
個別指導の第一フェーズでは電力使用量の削減、第二フェーズではデマンド削減をテーマにして進めていったといいます。
「それぞれのフェーズでは、開始から半年ほどで効果が出始めました」(齊藤氏)。
またその際のコミュニケーションのポイントについて齊藤氏はこう話します。
「自主性を尊重しながら、作業者が今欲しい情報をヒントとして提供します。こちらが全てやってしまうと達成感がなくなってしまい、自主的な活動につながりづらいからです」(齊藤氏)。
さらに省エネを妨げるさまざまな要因、いわゆる「省エネバリア」について、齊藤氏は省エネ雑誌に掲載されている一覧表を参考にしながら、教育時のアプローチを変えるといった地道な取り組みも続けました。
こうした電力のリアルタイムでの可視化に加えて、省エネマイスターによる個別指導によって、小集団による自主的な省エネ活動が所内に広がっていったのです。
省エネマイスターの資質
今回の施策で中心的な役割を担う省エネマイスターだが、具体的にどのような資質が求められるのでしょうか?
木下氏はこう説明します。
「(初代省エネマイスターの)齊藤はエネルギー管理士ですが、設備担当の技術資格も持っています。つまり電気や保全が分かることがベースです。それに加えて弊社で運営している省エネ会議などをしっかり運用するマネジメント力。さらにエネルギーに関する専門知識も兼ね備えることが重要です」。
エネルギー管理者と省エネマイスターの違い(出典:トピー工業資料を基にエネチェンジ作成)
今後の方針
今後は神奈川製造所の成功ノウハウを別の拠点に展開していく予定です。すでに昨年には各工場に省エネマイスターを配置したといいます。
「省エネマイスターを集めた会議を定期的に開き、神奈川製造所で蓄積したノウハウや事例を開示しているほか、各製造所の進捗を共有しあっています」(齊藤氏)
また木下氏はこうも話します。
「こうした会議は、齊藤が全体を取りまとめる形で進めています。さらに今年の10月からは、他の製造所でもエネルギーの見せる化を始めます。いかにして短期間で形にできるか切磋琢磨していきたいです」。
神奈川製造所で試行錯誤の末に獲得したノウハウを、全社に定着させるという新たなミッションに乗り出した形です。
補助金一覧シートのご案内
全国の各自治体によるエネルギー系補助金の一覧シートをダウンロードいただけます。下記フォームよりメールアドレスをご入力ください。(利用規約・個人情報の取扱いについて)