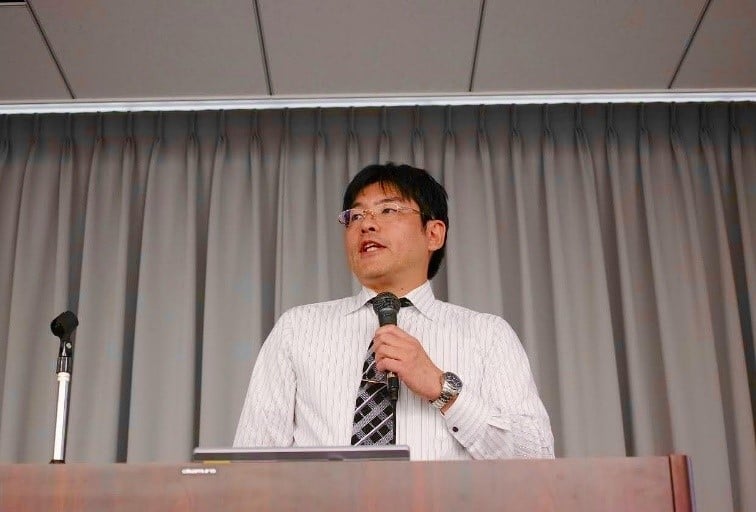
工場で使われる設備の中でも、電気使用量の上位を占めることが多いコンプレッサー。
金・銀系の素材・加工品を製造・販売する田中貴金属工業株式会社は、そのコンプレッサーの省エネ施策によって、2019年に省エネ大賞「審査委員会特別賞」を受賞しています。
施策の対象になったのは群馬県富岡市にある富岡工場です。
金・銀系の産業用母材工場として位置づけられる富岡工場では、板材や線材などのほか、自動車や産業用リレーなどに搭載されるリベット接点を生産しています。
2010年度から着実に省エネ施策が進められてきた同工場では、2018年度までの8年間で41%ものエネルギー削減(原単位)に成功してきました。
まずはインバータ設置によるポンプやブロアーの動力低減など、設備単体レベルの省エネから着手。5年以内の回収を目途に投資を進めたといいます。
さらに設備単体レベルで費用対効果のある省エネ施策が少なくなってきた2014年度からは、仕組みレベルでのより複雑な省エネ施策に乗り出しました。
中でも大きな成果につながった施策が、冒頭に挙げたコンプレッサーの省エネです。
この施策に携わった同社の木村真一(生産技術セクション)さんは、コンプレッサーの省エネ施策として次の4つを挙げています。
- 配管系統の見直し
- コンプレッサー本体の統合
- 昇圧専用コンプレッサーの採用
- コンプレッサーの土日停止
2017年度に実施したこれらの4施策による削減効果は年間230MWh。電気代にして約415万円に上るそうです。投資額は3年で回収できる見通しだといいます。
木村さんが「省エネ診断・技術事例発表会」(一般財団法人省エネルギーセンター主催)で発表した内容をお伝えします。
省エネターゲット、電気使用量が特に多いコンプレッサに注力
富岡工場にある各生産設備の動力源として、圧縮空気を送り出しているコンプレッサー。
数ある設備の中で、コンプレッサーを省エネ対象として選んだ理由は、その電気使用量の多さにあるといいます。
下の図は、工場にある設備ごとの電気使用量パレート図です。工場全体の生産設備やユーティリティ設備が対象になります。
電気使用量の上位5つのうち、3つをコンプレッサーが占めていることが分かります。
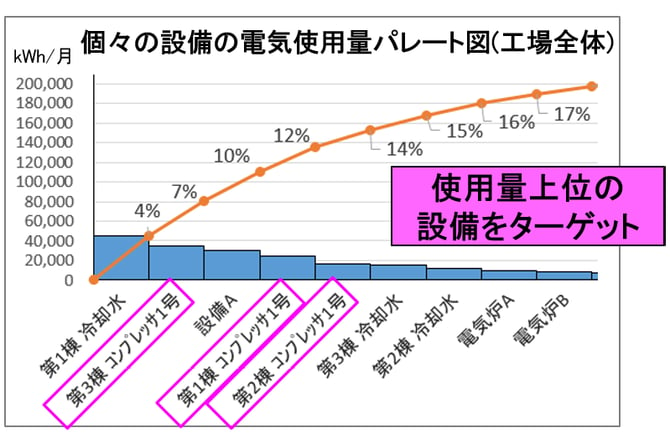
1.配管系統の見直し
この状況を踏まえて、木村さんらが着手した施策の一つが配管系統の見直しです。コンプレッサーによる吐出圧力の引き下げを狙いました。
吐出圧力を0.1MPa下げるごとに、一般的に8~10%の省エネにつながるといいます。
木村さんによると、今回の施策に着手する前から、吐出圧力の引き下げを幾度となく試みてきたといいます。
使用側でのエア漏れ対策やエアーブローノズルの改良・断続化のほか、未使用時は配管の元バルブを閉めるといった活動です。
ただエアブロー工程が工場全体で200か所以上に上り圧力損失が発生していたため、吐出圧力が0.67MPaに高止まりしていました。
そこで急激な圧力の低下を防ぐために、今回の施策では65A以上の主配管のループ化に着手しました。
これによってエア圧が安定し、コンプレッサーの吐出圧力を0.67MPaから0.58MPa以下に下げることに成功したといいます。削減効果は年間119MWhになりました。
2.コンプレッサー本体の統合
さらに合わせて実施した施策が、複数あったコンプレッサーの統合です。
富岡工場では、従来からエア圧の安定化を目的として複数のコンプレッサーを分散設置していました。
第2工場棟に1台(55kW)、第3工場棟に2台(37kW×2)のコンプレッサーを置き、それぞれの棟のコンプレッサーを連絡配管でつなげていたのです。
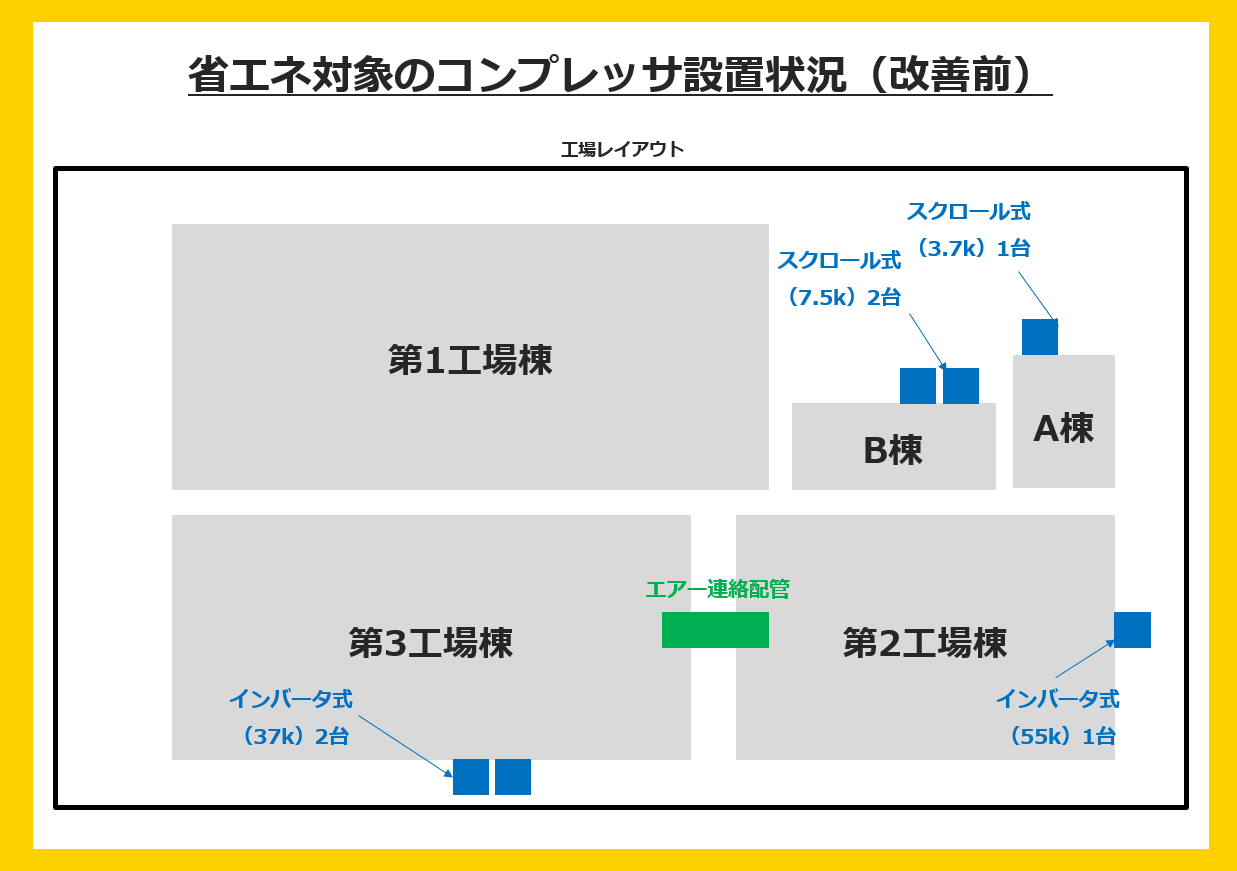
しかし2つの工場棟のコンプレッサーを合わせて、平日で平均102kWhの余裕があることが分かったといいます。
そこで第3工場棟にある37kwのコンプレッサー2台を、インバータ式の55kW1台に統合しました。
さらに運用改善にも着手。第2工場棟と第3工場棟にそれぞれ1台ずつ分散設置している中で、以下の要因から第3工場棟のコンプレッサーをメインとしてフル稼働させることにしたといいます。
- 第3工場棟のコンプレッサーはトップランナーモータ搭載機であるため
- 同棟はエアブロー工程が多いことから、圧力損失低減のため
一方で第2工場棟のコンプレッサーは、設定圧力を若干低めに設定。第3工場棟の圧力変動に対して、インバータ制御で追従させる運用にしました。
さらに改善前の段階では、A棟のコンプレッサー(スクロール式3.7k)はほとんど使用されていなかったことが判明。そこでA棟の3.7kを撤去したうえで、A棟とB棟をつなぐエア連絡配管を新設して両棟のコンプレッサーを統合しました。
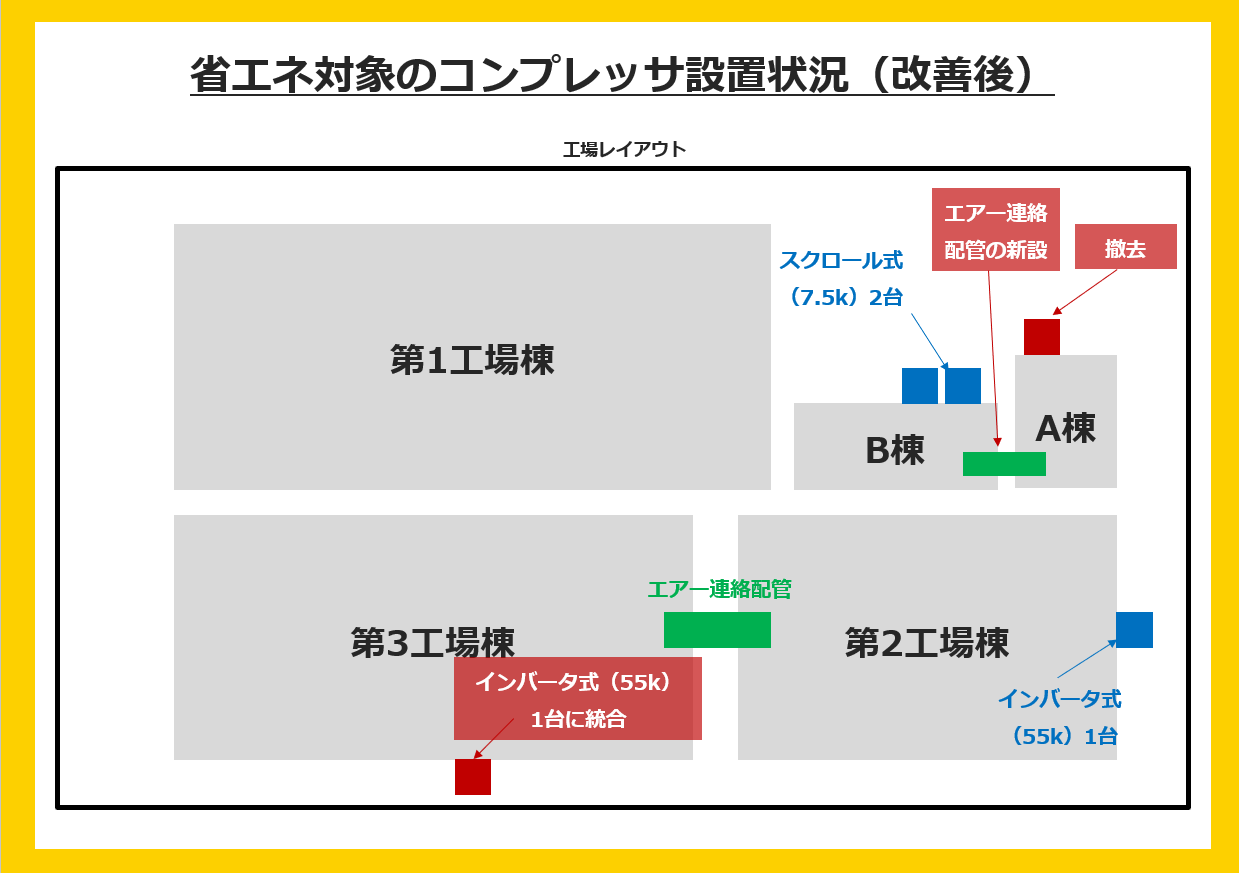
これら一連の施策によって、年間69MWhの削減効果があったそうです。
3.昇圧専用コンプレッサーの採用
3つ目の施策は、昇圧専用ベビーコンプレッサーと切替式省エネ制御の導入です。
表面研磨装置が必要とする圧力に応じて、柔軟に圧力を変動させることによる省エネ効果を狙いました。
従来の研磨工程では、高圧設定のコンプレッサー3台(7.5kW×3)を活用していたといいます。通常運転では0.5MPaで研磨し、研磨しきれない場合は0.7MPaまで手動で昇圧していました。
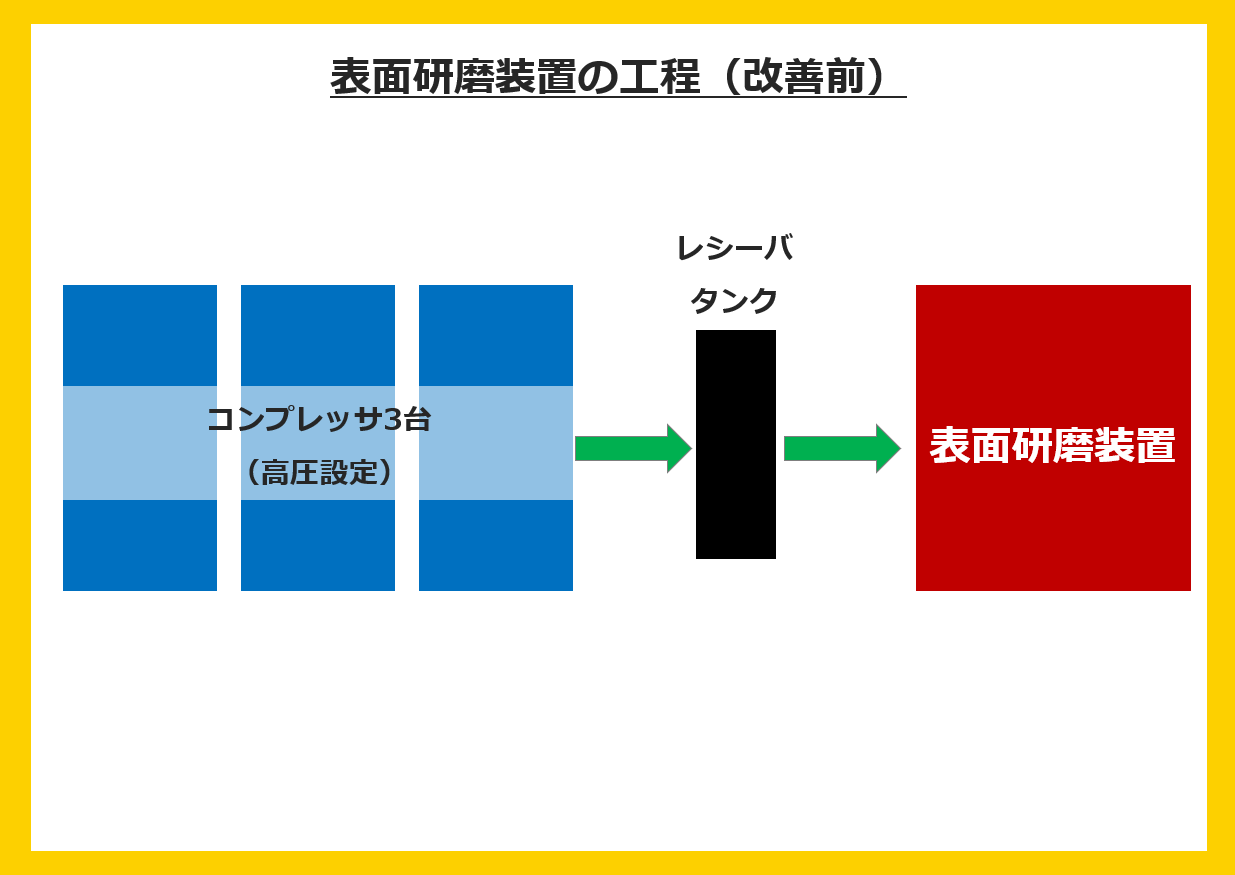
ただ3台の検証テストをしてみると、コンプレッサーの待機電力にムダがあることが判明したほか、今後さらに生産性を上げることを考慮した場合に、流量の引き上げに限界があることもわかったそうです。
設置スペースの関係上、レシーバタンクの大型化も難しかったといいます。
改善後は、まず第2工場棟のコンプレッサー(55kW)に対して、0.7MPaまで昇圧できる昇圧専用ベビコン(11kW)を組み込むことで、必要最大圧力を達成できる状態をつくりました。
また必要に応じて圧力を調整できるよう、切替式省エネ制御も導入しています。
木村さんによると、使用状況として0.5MPaでの研磨が全体の8割、残り2割が0.7MPaということがわかったといいます。
そこで0.5MPaで研磨する際は第2工場棟のコンプレッサー(低圧)、0.7MPaで研磨する際は昇圧専用ベビコン(高圧)を活用するという切替式にしました。メインルートである0.5MPaを使用する際は、昇圧ベビコンを停止する操作を手元でできるようにもしています。
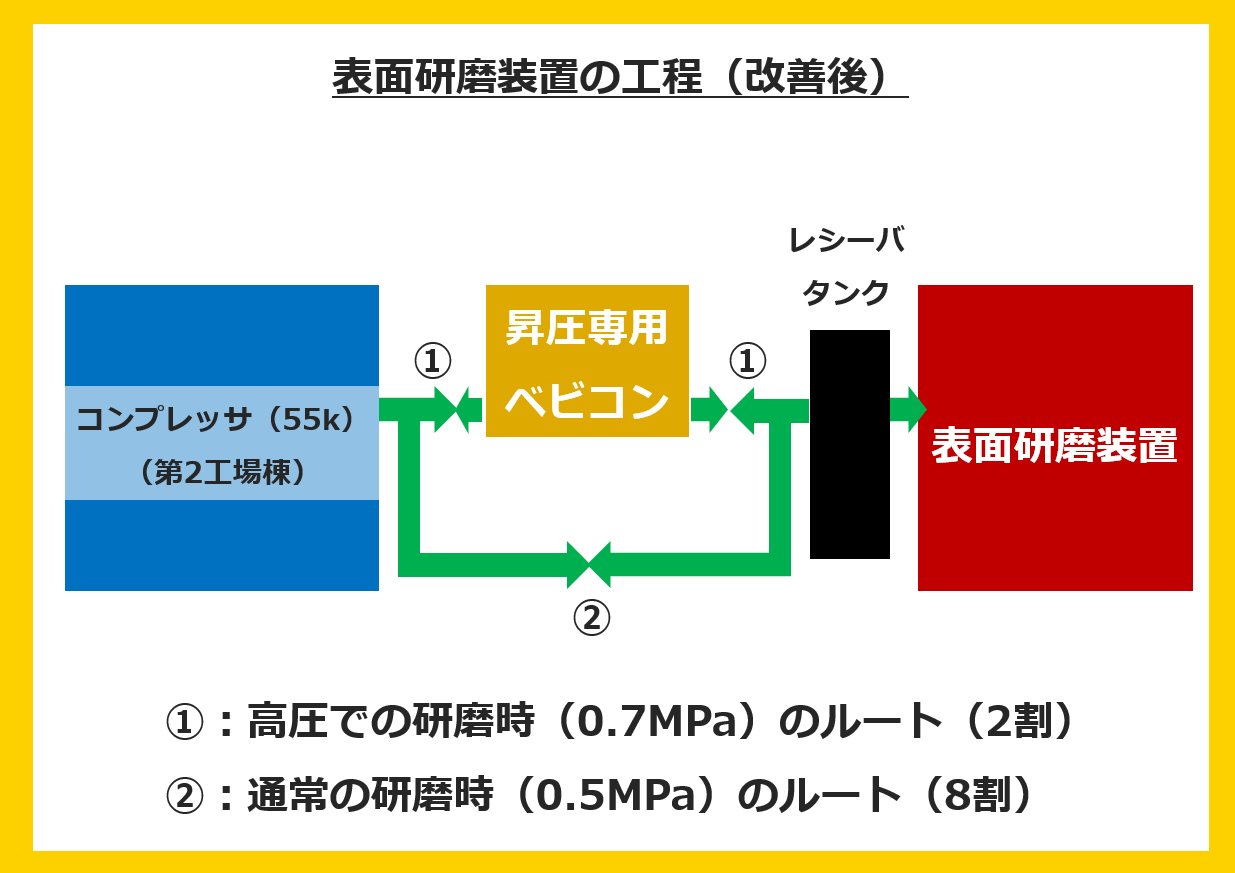
一連の施策による省エネ効果は年間17.3MWhほどだといいます。
4.コンプレッサーの土日停止
さらに同じく2017年度からは、コンプレッサーの土日停止にも着手しました。これは生産性向上や品質改善などを目的とした「TOTALエコ活動」を始めたことで、初めて可能になったといいます。
当初は1台の遠隔操作盤によって自動停止させる想定だったものの、操作対象が6工程と広範に及んだだめ、運用が難航したといいます。
自動停止といっても実際に稼働が止まるのは操作から最大7時間後になってしまう点や、夜に従業員が停止作業をすることで、照明や空調のムダが発生してしまうといった課題が表面化してきました。
そういった状況を踏まえ、改善策として停止用のカウントダウンタイマー付きの遠隔操作盤を計4エリアに設置。
それによって各工程責任者が自らの管轄内で停止作業を実施できるようになりました。停止作業の運用が施設管理部門から使用部門へ移ったことで、よりムダのない停止運用ができるようになったほか、夜間などでの変則作業がなくなったため働き方改革にも寄与したといいます。
また遠隔操作盤の運用にも工夫があります。
消し忘れを防ぐために照明や空調の近くに設置したほか、新規に設置した集中制御盤によって、各カウントダウンタイマーの運用状況を見える化。コンプレッサーの停止時間拡大に向けて、対応すべきボトルネック工程を探すことも可能になりました。
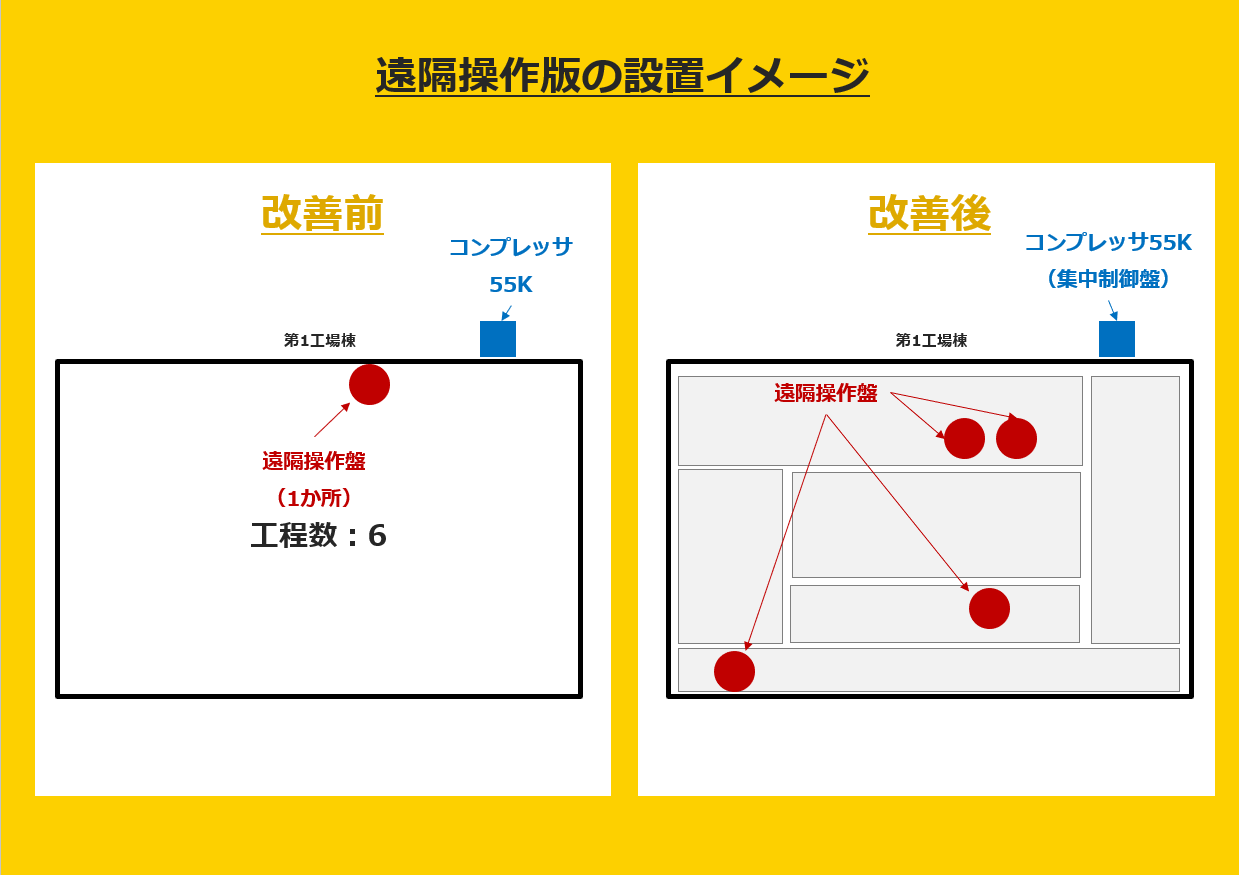
「永続的にエネルギーを削減できる工場を目指している」と話す木村さん。
今後は電気炉による廃熱利用の強化や、セントラル空調から個別空調への入れ替えなど、さらなる省エネ施策を予定しているそうです。
補助金一覧シートのご案内
全国の各自治体によるエネルギー系補助金の一覧シートをダウンロードいただけます。
下記フォームよりメールアドレスをご入力ください。いただいたアドレス宛に資料をお送り致します。(利用規約・個人情報の取扱いについて)